Are you wondering what is “Rockwell hardness of steel” is? Well in simple words, it determines the effect of heat treatment on the steel. And manufacturers use this to measure the hardness of the steel.
Hugh Rockwell and Stanely Rockwell co-invented this in 1914. They came up with the idea of using a cone-shaped diamond with 150kg weight and pressing the whole thing against steel. With this, they figured how much the steel can handle before getting distorted and penetrated. This is how they did the hardness test of steel and that is what we call today HRC or the Rockwell Scale.
so in easy words, we can say to find out how resistant a steel metal is, how much it can handle before getting fully deformed is what the whole concept of Rockwell hardness. This measuring system is non-destructive metallurgical testing. And through this, you can find out how hard and strong steel is that used in knife-making.
Steel Hardness rating has a predetermined chart that has to be followed by every knife blade manufacturer. It’s called the Rockwell C scale. To accurately indicate the hardness of the metal, engineers use this differential depth machine -Rockwell Hardness tester. The higher the number of Rockwell hardness ratings, the harder the steel is. Contrarily, the lower the number of Rockwell hardness ratings, the softer the steel is.
A misconception that most people have is better quality knives have high. Every knife steel has a certain HRC. Most knife blades in the market have a Rockwell rating from 54 HRC To 64 HRC. Most of the time we assume the higher the HRC the stronger the knife is. This is incorrect. A steel’s hardness is increased by considering the toughness of the steel. While producing a knife blade, knife makers decide on the steel’s hardness on the basis of the true purpose or use of the knife blade.
As a rule of thumb, we have seen that softer steel with rockwell rating in between 45-54 has more durability and better resisting capability than hard steel with rockwell testing rated at 60-64. When higher hardness the steel loses its toughness and vice versa. For instance, a kitchen knife and a hunting knife have different purposes.
For a kitchen knife, we prefer high hardness with steel Rockwell hardness 60-62 or more for greater edge retention, and for a hunting knife, a camper would prefer something that has a lower HRC so that can be easily sharpened. For edge retention hard steel is better. Soft steels do not hold their edge longer. They are more prone to getting chipped and pitted when roughly used.
WHO USES THE ROCKWELL HARDNESS SCALE AND WHY
Every steel manufacturer in the world uses the Rockwell hardness scale. The HRC scale is the industry standard, for steel products such as ball bearings, tool steel, and knife blades. In the USA there are two industry authorities that determine Rockwell testing of steel. They also established how to conduct the hardness testing in the right way. Every steel manufacturers in the industry rely upon the hardness testing method of :
- American Standard Test Method for Rockwell Hardness and Rockwell Superficial Hardness of Metallic Materials (ASTM E 18 Metals)
- International Standards Organization – Rockwell Hardness Test Part 1 – Test Method (ISO 6508-1 Metallic Material)
To ensure steel quality all steel product manufacturers use the Rockwell hardness scale. Before dispatching the steel products, the makers have to confirm uniformity in test results. Everyone in the steel industry is very much familiar with the Rockwell hardness of steel. They can figure out the steel strength from just a glance at its Rockwell rating. The Rockwell system is universally recognized as a hardness baseline. That’s particularly so in knife blade manufacturing.
Blade manufacturers design their products Rockwell hardness number according to the blade’s specific usages. Experienced knife makers endeavor for a hardness rockwell between soft Rockwell scale steel and hard Rockwell scale material. That makes the knife steel more durable and with good corrosion resistance.
Knife manufacturers determine a specific steel strength to get the right steel for the purposeful application. Then the engineers test it to ensure the blade meets an exact number on the Rockwell hardness scale.
What do Rockwell Hardness Numbers Mean?
Rockwell hardness numbers measure the surface hardness of metals and other materials. They’re typically given as a number ranging from 0 to 100, and they’re measured by using a stylus that presses down on the metal or other material at different places. The harder the metal, the higher its Rockwell hardness number will be.
What is Rockwell Hardness Test?
The Rockwell hardness test measures the resistance of a material to indentation. The indentation is made with a standardized ball indenter that has a flat circular shape and a radius of 25.4 mm or .01 inches at its largest diameter. The ball indenter is pressed against the surface to be measured at a constant rate of 0.7660 kg per square inch so as to not exceed 5 pounds pressure.
Rockwell Hardness Chart for Metals/Steel
The Rockwell Hardness Chart for Metals is a chart that has been used extensively in the engineering and manufacturing industries. The Rockwell Hardness Chart for Metals was created by Harold F. Rockwell in 1900s. This chart can be used to test the hardness of metal-based on how hard it is to indent the metal under a given load with a diamond point indenter.
Steels | HRC |
---|---|
CPM S110V | 58-61 |
CPM S90V | 57-59 |
M390 | 59.6 -60 |
ZDP 189 | 64-65 |
Elmax | 61-63 |
CPM-20CV | 59-61 |
CTS XHP | 60-64 |
CPM M4 | 62-64 |
CPM S35VN | 58-61 |
CPM S30V | 58-60 |
154CM | 58-61 |
ATS 34 | 59-61 |
D2 | 60-62 |
VG-10 | 60-62 |
H1 | 58-60 |
N680 | 56-58 |
440C | 58–60 |
AUS-8 | 58-59 |
CTS BD1 | 58-60 |
8Cr13MoV | 58-60 |
14C28N | 55-62 |
440A | 55-58 |
420HC | 56-59 |
13C26 | 55-62 |
1095 | 56-58 |
420J | 56-58 |
AUS-6 | 59-60 |
Maxamet | 67-68 |
CruWear | 60-65 |
Knife Rockwell Hardness AKA HRC
Be it industrial machine knives or kitchen knives, to make sure they perform properly and profitably, knife makers have to go the extra mile while selecting the appropriate steel hardness which is very important. You must know, steel strength isn’t related to quality.
Usually, all Knife blades are of the highest quality, produced with high-grade steel. As a part of the quality control process. Knife steel manufacturer uses Rockwell hardness testing on all customers’ blades. Most steel alloy in knife blades ranges from HRC 45-60 category.
Now if someone wants a soft steel blade in the Rockwell hardness number 40 range, the tech department needs to test it and verify it before shipping the alloy from the factory. Likewise, if a customer orders tough blades with flexible hardness in the Rockwell hardness number 60, the manufacturer company has to verify the rockwell hardness scales measure 60 range of those blades to meet the customer’s needs.
Best Rockwell Hardness For Knives
Before we divide into this, I want to make it clear that, there is no perfect Rockwell hardness for a knife as it totally depends on the knife’s purpose. The indentation hardness is depended on various factors. For instance, a kitchen knife’s purpose isn’t the same as a camping knife.
But when it comes to kitchen knives, the HRC rating plays an important role. Let me tell you how. Bald that has HRC 45 will be made of softer steel . This will be very easy to sharpen but it won’t hold a greater edge so the blade needs to be sharpened often.
Again blade with HRC 62 or above will be made of harder steel. And such a blade with harder steel is much likely to get broken under pressure.
Chefs prefer a knife with higher hardness from HRC 60-64. As they know their knives and can handle them well, they care about greater edge retention. Similarly, hunters prefer knives with low HRC so that they can easily sharpen the knife whenever they want but use the knife as roughly as possible.
But what kind of knife is good with this steel is the real question. As I mentioned above it truly depends on your usage.
My two cents? Well, your best choice for finding a great quality kitchen knife would be to go for knife steels with a hardness rating around 58 to 60. You can find an HRC60 knife with Damascus steel, premium VG10, and Japanese stainless steel. They offer extremely durable blades with higher wear resistance and incredible holding edge ability. Thus it will be easier for you to handle your knife as well as maintain them for a long period.
Conclusion
Before buying a knife, always check the Rockwell hardness. It’s a great factor to look up to as it will give you a clear idea about the knife steel. As I can’t stress enough how high HRC doesn’t necessarily mean a better knife, so don’t just go with the high Rockwell hardness number.
Rather know about the blade steel, its potentiality, and what you really want to do with your knife. Define the expectations you have from your knife and by reading about the knife blade, find the best choice for you.
In this way, you won’t end up buying a 300 dollars knife which is totally wrong for you instead of getting the 40 dollars knife that you need. That’s how you can shop smart and save your money. You’re welcome!
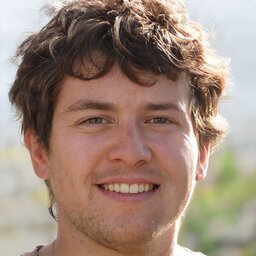
Hi, my name is Taras Kulakov and I’m a knife enthusiast. I have been collecting knives for over 30 years and I’ve owned literally thousands of different models over that time. My goal with this site is to share some of what I’ve learned about knives. You can find more info about Taras Kulakov here.